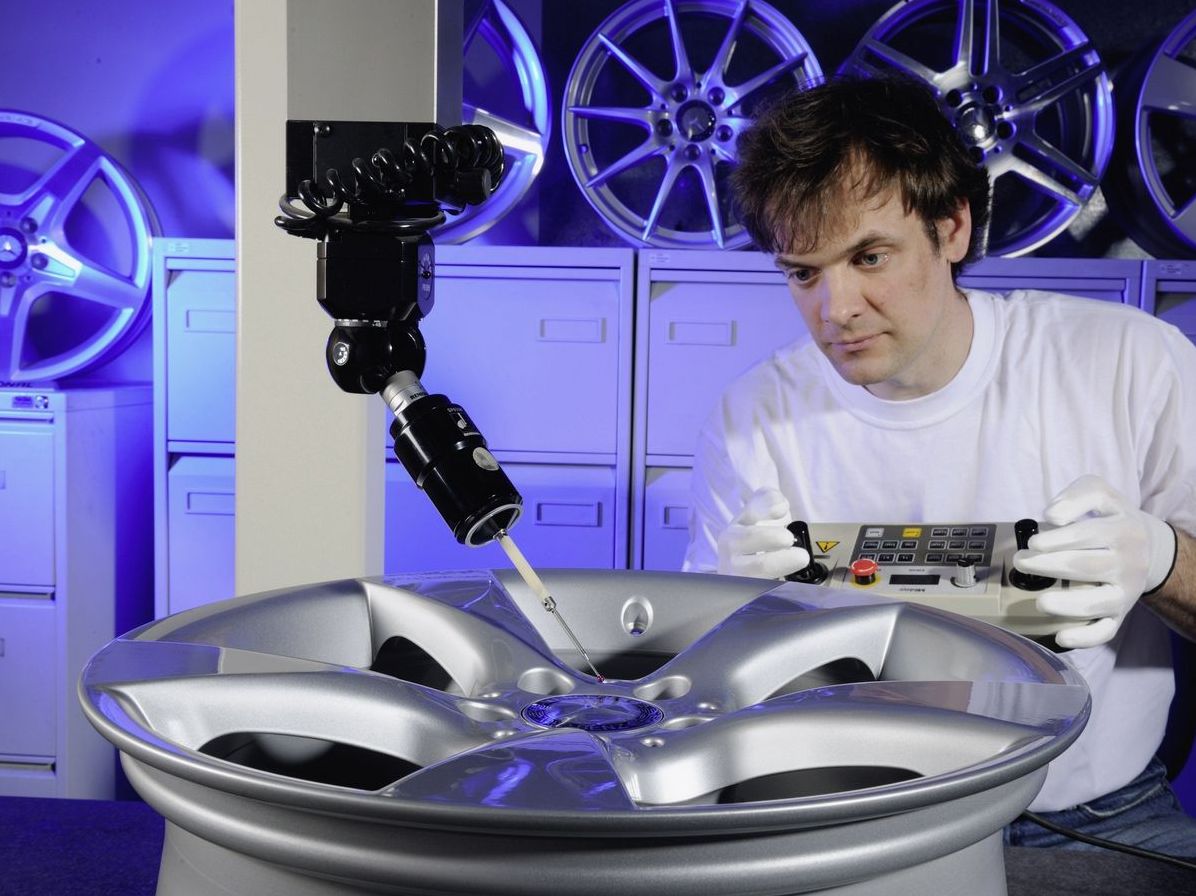
Технології потроху змінюють світ. Ми звикли купувати деталі машин через складні логістичні схеми із замовленням потрібної запчастини на іншому краю світу. Вибирати постачальника і гадати про застосовувані технології. Напевно траплялися і підробки, і просто невдалі екземпляри. І завжди чекати, чекати, чекати. Зовсім погано тим, у кого машина рідкісна. Запчастини «зі складу» доводиться шукати довго. Але ситуація буде змінюватися. Ба більше, вона змінюється просто зараз.
Не так давно компанія Daimler-Benz запустила промисловий 3D-друк металевих компонентів із легких сплавів. Наприклад, корпуси термостатів роблять саме таким чином. Причому деталь виходить практично готовою, не потребуючи додаткової обробки, тільки зняття технологічної опори. А пластикові деталі «друкують» уже давно.
Саме час розібратися, що таке 3 D друк, який він буває, і з чого зроблені деталі, створені з його допомогою. І головне, чим нам загрожує застосування нових технологій у найближчому майбутньому.
Не можна сказати, що 3 D друк — технологія нова і невідома. З’явився він понад 30 років тому, а зараз друк металевих деталей у великих масштабах використовується в медичній промисловості для створення біопротезів, у ювелірній справі та навіть в авіації.
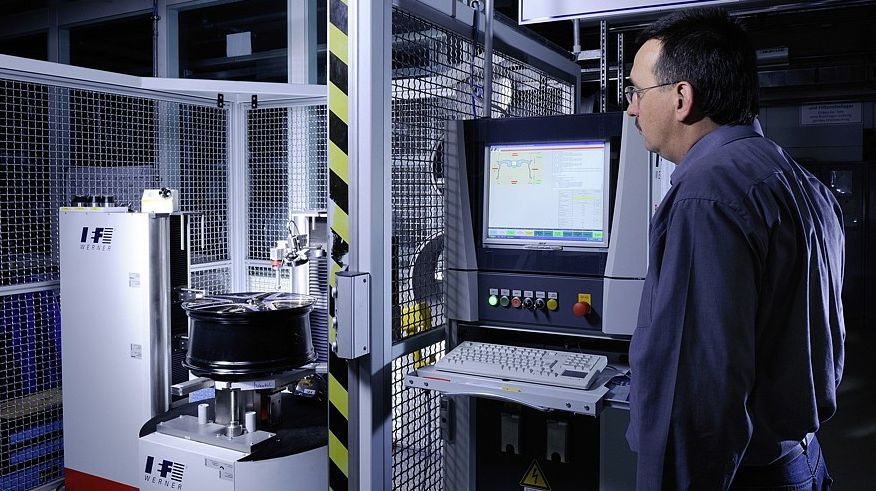
Не обійшлося без цієї технології у справі виготовлення дослідних зразків автомобільної промисловості. Солідна частина дослідних зразків машин на виставках і тестових екземплярах вироблена з використанням цієї технології тією чи іншою мірою. Причому застосовується вона як для створення вже «готових» виробів — роздільна здатність 3D-принтера дає змогу отримати готову продукцію — так і для подальшого високоточного механічного оброблення. Так створюють деталі циліндропоршневої групи перспективних моторів або коробок передач.
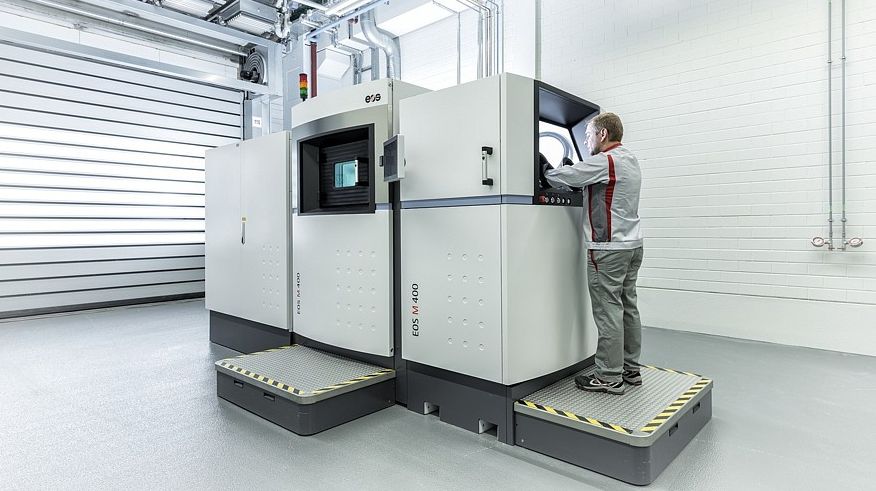
Собівартість «надрукованих» деталей
Традиційно вважається, що ціна друку металевих, та й пластикових деталей на 3 D принтері набагато вища, ніж ціна «звичайного» виробництва. Але ситуація змінюється, і собівартість виробництва, і постачання традиційними шляхами, і безпосередній друк підійшли до межі, після якої ситуація зміниться незворотньо.
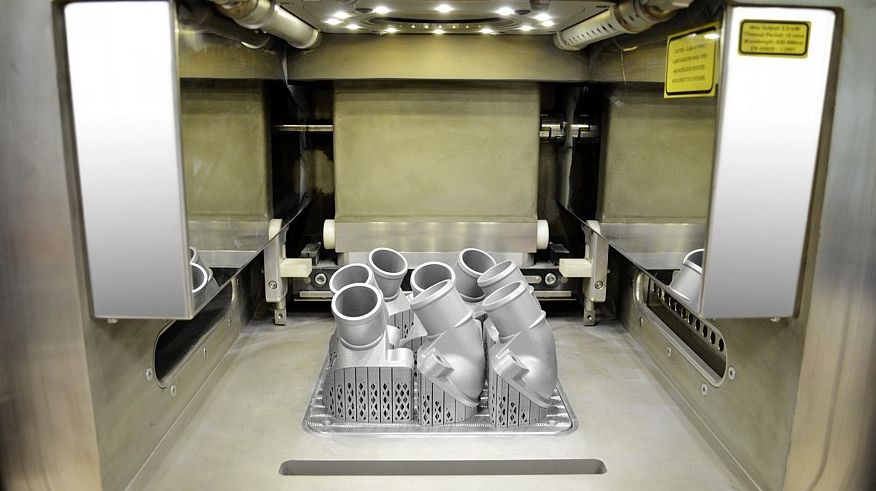
Треба зауважити, що ціна будь-якої речі в нашому оточенні зовсім не дорівнює її собівартості. І навіть не собівартості разом із прибутком виробника. У ціні закладена вартість постачання, логістики, а часто ще й тривалого зберігання. Усі ці фактори разом підвищують ціну в кілька разів, а у випадку з недешевими великими деталями, що вимагають особливих умов зберігання і транспортування — навіть на порядок або два. І це ми навіть не намагаємося враховувати витрати на маркетинг, підтримку і розробку.
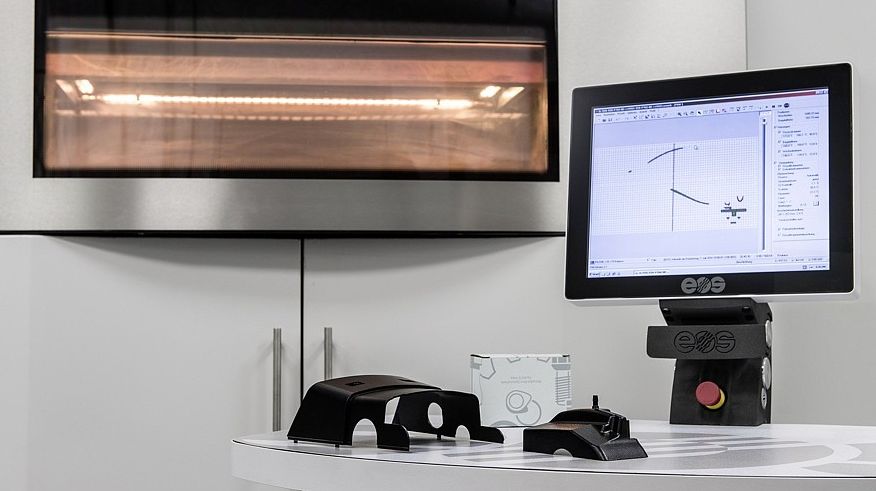
Загалом, традиційне виробництво дійсно максимально ефективне, особливо за великих обсягів випуску. Але сама система постачання потрібних компонентів уже набагато складніша, і тому з’являються ніші, в яких вкрай ефективною виявляється технологія, що дає змогу виробляти деталі малими обсягами безпосередньо на місці виробництва. Зокрема, в єдиному екземплярі або з численними модифікаціями. Наприклад, за допомогою 3 D принтера…
Виготовити рідкісний варіант однієї з деталей автомобіля за наявності креслення набагато простіше, ніж шукати компоненти в хорошому стані на авто двадцятирічної давності. Особливо якщо деталь одна з тих, що найчастіше ламаються, а машина рідкісна. З використанням 3 D сканування можна створити образ деталі «за збереженими уламками» або на основі дзеркального її варіанту.
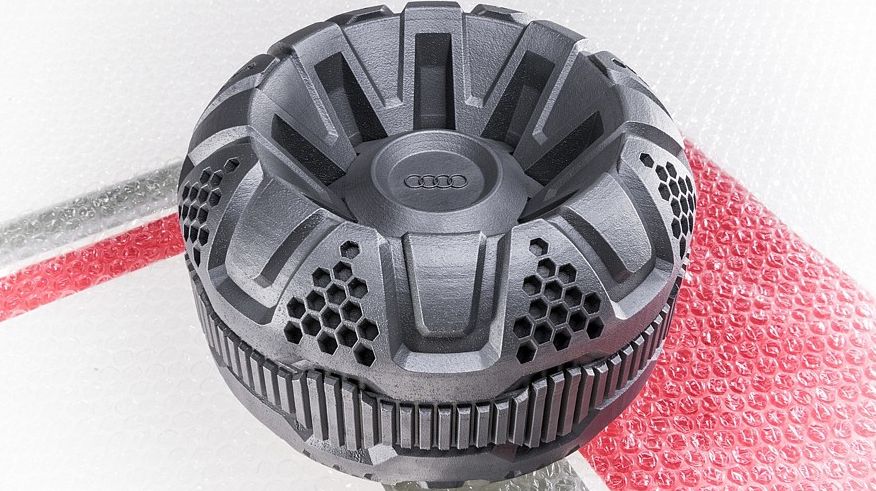
![]() |
![]() |
![]() |
Ще дуже зручно вносити зміни: посилити слабке місце корпусу, прибрати зайві елементи або ще щось подібне… І головне, не потрібно створювати запас деталей, які, можливо, ніколи не знадобляться. Буде достатньо матеріалу, принтера і 3 D моделі в цифровому вигляді.
Основні постачальники програмних CAD-продуктів давно оптимізували їх для роботи з технологіями тривимірного друку, тож уперше реалізується ідеальна формула виробництва: з креслення одразу в готовий виріб. Але ж лиття і мехобробка вимагають безлічі додаткових зусиль, створення різних пристосувань та інфраструктури… З тривимірним друком же виходить майже «за щучим велінням» — і ось готовий виріб.
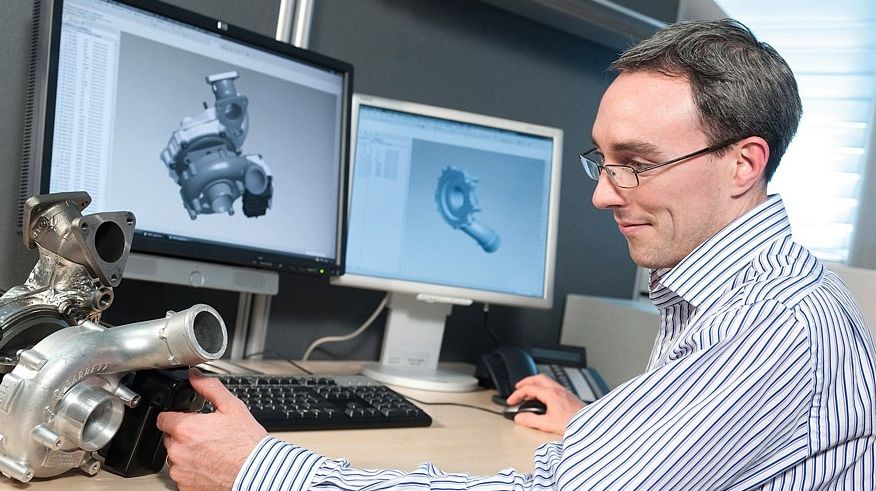
Масове виробництво також має безліч «екологічних ніш» для 3 D технології. Об’ємні деталі складної форми, наприклад, за ціною можуть виявитися навіть дешевшими, ніж вироблені класичним способом за допомогою лиття або з цільної заготовки. Особливо якщо йдеться про розміри понад метр за високої точності виготовлення.
![]() |
![]() |
Тонкостінні деталі з легких сплавів також може виявитися дешевше «надрукувати», ніж відлити. Це не кажучи вже про виробництво пластикових елементів і деталей малих серій. З розвитком нових технологій з’явиться можливість помітно поліпшити пасивну безпеку машин завдяки введенню вузлів з ідеальним розрахунком енергії поглинання, використовувати набагато компактніше розташування агрегатів і взагалі дати волю фантазії.
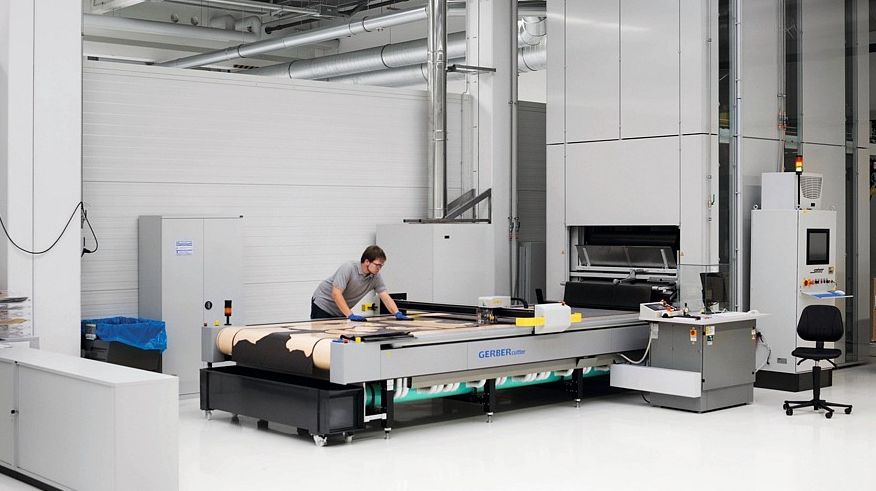
Ставлення до 3 D друку як до «несерйозної» технології пора залишити в минулому. Вироблені за її допомогою металеві деталі за характеристиками міцності не поступаються звичайним литим, хоча використовують дещо дорожчі сплави. Але ціна матеріалу вища зазвичай на 15-20%, а втрати під час друку менші в кілька разів. Та й з розмірами все чудово, в Амстердамі «друкують» справжній пішохідний міст завдовжки близько 30 метрів.
Матеріали для 3D друку
Основна маса деталей, зрозуміло, — поки що пластик, але сплави металів і різні види бетону також використовуються під час 3D-друку. Для автомобільної промисловості найцікавіше саме пластик і метали. І вибір матеріалів досить великий. Найперспективніші для застосування сталь і алюміній, але в машинах багато електричних вузлів, провідників складної форми та інших елементів, для яких стала б у пригоді мідь.

З металів у 3 D друку найпопулярнішим залишається титан. У нього чудові характеристики міцності, і він затребуваний у сфері протезування, в космічній та авіапромисловості, які поки що лідирують у застосуванні технології, що нас цікавить.
Нержавіюча сталь з високим вмістом кобальту і нікелю також чудово підходить, і ціла низка промислових принтерів працює з цим матеріалом, благо він порівняно недорогий. Звісно, він у рази дорожчий за найдешевші сорти сталі, але, проте, помітно дешевший за кольорові метали. А міцність виробів зі сталі вам напевно відома.
Алюміній як матеріал для 3 D друку набирає популярності. Вироби з нього легкі, мають гарну стійкість до корозії на відкритому повітрі, плюс він зручний в обробці і знову ж таки недорогий. Порівняно невисока початкова ціна установок, що працюють із цим матеріалом, також важлива. Він використовується в «домашніх» технологіях металевого 3 D друку, доступних малим підприємствам. На жаль, у порошковому стані він вибухонебезпечний, як, утім, і титан.
Кобальт-хром та інконель — це приклади спеціалізованих сплавів для 3 D принтерів стоматологічного, медичного та аерокосмічного призначення. Подібних матеріалів стає дедалі більше. Спеціальні матеріали для нової технології з’являтимуться й надалі, у міру розвитку технології потрібно зайняти все більше ніш.
Мідь, золото, срібло — також вельми поширені матеріали для 3 D друку. Зрозуміло, поки що це переважно друк ювелірних виробів. Але мідь і срібло також знайшли застосування як матеріал для виготовлення монтажних плат для електроніки. Щоправда, для цього часто використовують не «справжній 3 D», а такий собі «2,5 D» принтер, що створює деталі з висотою рельєфу в межах кількох міліметрів на керамічній підкладці.
Технології 3 D друку
Що стосується технологій, то для масового виробництва найактуальніші найдорожчі EBM і DED технології. За незрозумілими абревіатурами ховаються Electron Beam Manufacturing (формування виробу з порошкового металу під впливом пучка електронів) і Directed Energy Deposition (осадження металу з порошку або дроту під впливом лазерного променя або плазмової дуги). Обидві технології дають змогу створювати вироби з якістю металу вищою, ніж у литва, з ідеально однорідною структурою і з високою точністю.
EBM формує розплав у чітко визначеній зоні, а DED буквально «вибиває» розплавлений метал на потрібну поверхню. Обидві технології можуть використовуватися не тільки для створення нової деталі, а й для відновлення вже наявної. Обидві технології дають змогу змінювати склад матеріалу в об’ємі, робити поверхню твердішою за основу, зміцнювати особливо вразливі місця і тому подібні «фокуси».
Основна проблема — швидкість роботи. Так, серійна машина Insstek MX3 з технологією DED має робочу зону розміром 1000 x 800 x 650 мм з товщиною шару в 0,089-0,203 мм, а швидкість роботи близько 2 шари за хвилину. Альтернативний Arcam Q 20 Plus має робочу зону 350 х 380 мм, точність виготовлення деталі до 140 нм і швидкість роботи близько 4 літрів об’єму деталі на годину.
Більш масова і менш точна технологія SLM / DMLS теж має хороші перспективи. Саме технологія SLM — selective laser melting, тобто, вибіркове лазерне плавлення, застосована компанією Mercedes-Benz для виробництва автомобільних компонентів. Споріднена технологія SLS — selective laser sintering, що означає «вибіркове лазерне спікання», застосовується для пластмасових деталей.
Причому компанія має намір таким чином постачати деталі не тільки для нових, а й для своїх класичних автомобілів. І це буде справжній «оригінал», тільки абсолютно новий і такий, що пройшов усі тести. Усі ці технології засновані на пошаровому спіканні об’єму порошку лазерним променем. Якість матеріалу в цьому випадку нижча, ніж у EBM/DED технологій, і деталь буде строго однорідною. Але, тим не менш, на виході якість не нижча, ніж у звичайного лиття і штампування.
Техпроцес DMLS досить простий. У робочу камеру подається необхідна кількість металевого порошку, його шар розрівнюється дозатором і видаляється зайвий матеріал. Після чого лазер «запікає» матеріал за необхідним контуром, а зайвий матеріал знову ж таки видаляється. Знову і знову, цикл за циклом, з точністю близько 20 мікрон і з товщиною шару до 100.
Технологія безвідходна і досить швидка. Уже доступні серійні принтери, що мають швидкість вище 9 кілограмів на хвилину, а можливості розпаралелювання процесу дають змогу значно її підвищити. Ось тільки вартість обладнання зростає в геометричній прогресії слідом за габаритами деталей. Саме за такою технологією виготовлено зі сплаву інконель деталі двигуна Super Draco (зокрема, камери згоряння) компанії SpaceX Ілона Маска, який автомобілістам більше знайомий як творець Tesla .
Для невеликих обсягів непогано підходить значно дешевша технологія Binder Jetting. Ця технологія цікава тим, що застосовується для створення не тільки металевих деталей. Деталь по суті створюється з частинок будь-якого матеріалу, склеєних між собою. Але якщо використовується метал, то після створення її можна «пропекти», і металеві частинки утворюють єдине ціле. Якість матеріалу, звісно, значно нижча. Але технологія помітно дешевша за інші і дає змогу створювати деталі з композицій матеріалів.
Схожа технологія використовується в найдоступнішому 3 D принтері для друку металевих деталей — Mini Metal Maker, ціною близько 1 600 доларів. Щоправда, точність уже не 20 і не 100 мікрон, а щонайменше 500. Зате розміри майже не обмежені, адже не потрібен ні вакуум, ні особливе середовище в робочій області.
Що в підсумку?
Прогрес у царині тривимірного друку йде настільки швидко, що протягом буквально десятка років можлива революція в галузі виробництва автокомпонентів і логістики під час її обслуговування. Навряд чи з’явиться можливість «роздрукувати» собі машину, але те, що традиційний ринок запчастин поступово зникне — це напевно.
Ми згадуватимемо вже не якість постачальників, а якість принтерів і цифрових моделей. Дізнаємося, що таке DRM стосовно креслень деталей. Ну і зможемо, нарешті, виготовити потрібну деталь «точно таку саму, але із золота і з інами». А які можливості відкриються у тих автолюбителів, які не проти щось змінити в машині куди більш кардинально! Загалом, на нас чекають цікаві часи. Бережіть себе.